
Pulmuone Foods USA
Mitigating surcharge hikes with onsite treatment of high-strength wastewater from food manufacturing
Pulmuone Foods USA, located in Fullerton, California is a food manufacturer, known for its organic tofu, processes primarily for soy-based products and is expanding its production capacity to meet increasing consumer demand in the U.S. The planned expansion will double its generated wastewater and increase forecasted surcharge fees.
Through its feasibility studies, Tomorrow Water has worked closely with Pulmuone to determine the best option to treat wastewater and mitigate the expected surcharge hikes, while minimizing waste at the same time. With the proposed new system, Pulmuone will be able to reduce the surcharge fees, which will recover the investment of the system within several years.The system will be designed and constructed by Tomorrow Water within a period of 14 months and presents a turnkey solution for Pulmuone - Tomorrow Water will also be operating the system upon completion.
The system will be designed and constructed by Tomorrow Water within a period of 14 months and presents a turnkey solution for Pulmuone - Tomorrow Water will also be operating the system upon completion.
-
Due to population growth and urbanization, increasing flows were straining Jungnang WRRF’s treatment capacities. Simultaneously, the facility
working to meet new stormwater and nutrient discharge goals
Since the Jungnang WRRF is located directly in the megacity of Seoul, it is extremely limited in expansion options and finding available land for new process equipment proposed a major challenge.
their treatment train to process more wastewater, to a higher quality, in a smaller footprint.
-
This process replaced a traditional primary settling, MLE activated sludge, and secondary clarifier process with a novel treatment train based on the Proteus biofilter. In the new design, screened and degritted municipal sewage is passed through three sequential upflow biofilter stages.
Following the three biofilters, effluent is flocculated and filtered using a membrane disc filter for total phosphorus control, followed by UV disinfection and discharge to surface waters.
The installation also includes a separate 500m3/day wet weather flow biofilter train to manage dilute stormwater influx
-
The new treatment train has operated at full capacity since September of 2017. Over 6 months, hydraulic residence time (from primary through tertiary treatment) averaged 3.5 hours, a 70% reduction from the previous average of 11 hours.
The footprint of the new treatment train was reduced by 64%. Primary treatment alone achieved a 50% reduction in suspended solids, at an HRT of 10.6 minutes, representing an 80% footprint reduction. These reductions were achieved using an innovative, high-loading filtration media, while overall treatment costs for the new process were not significantly different from traditional MLE processes.
Moreover, the entire train was constructed underground, and a public park was built above the site.



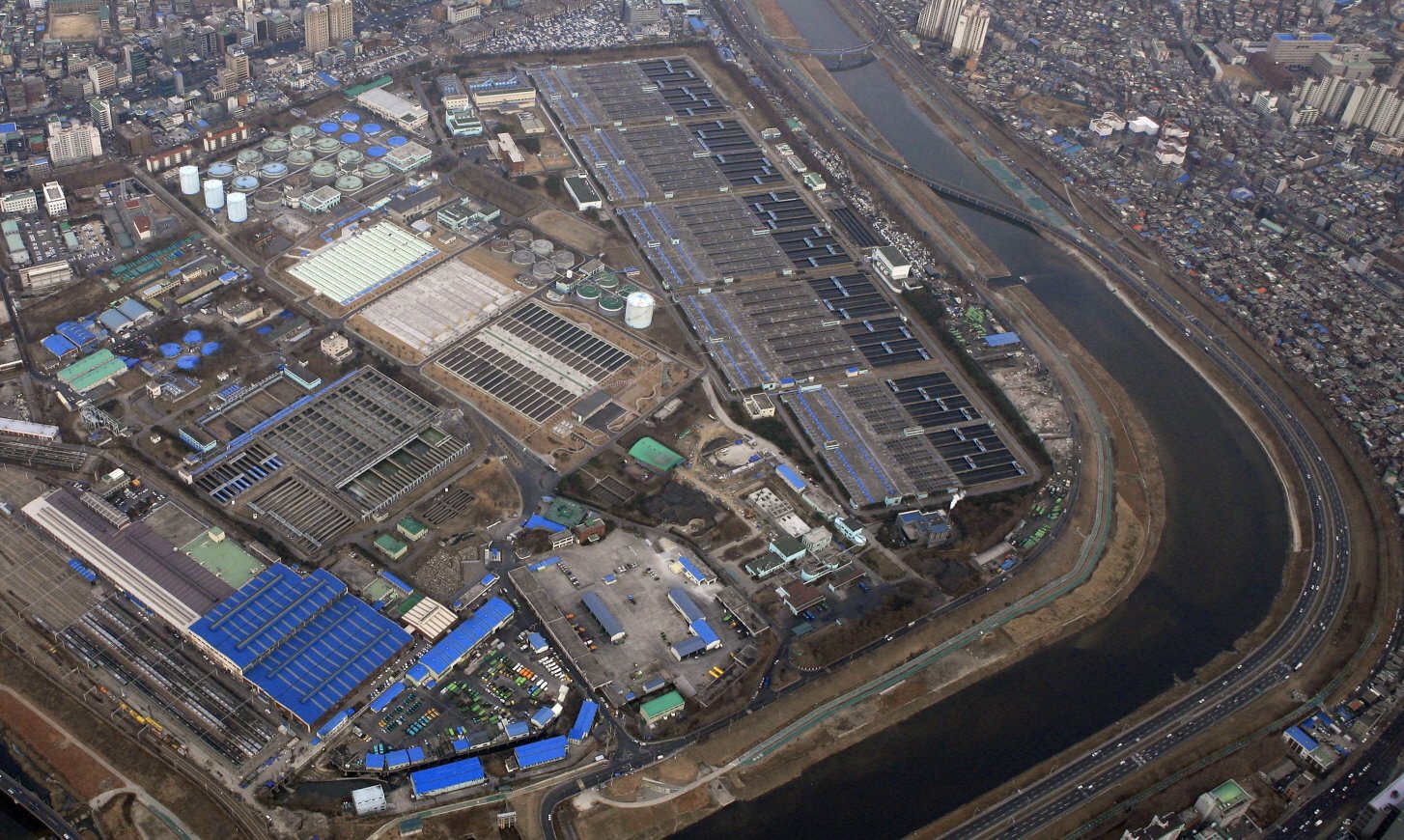
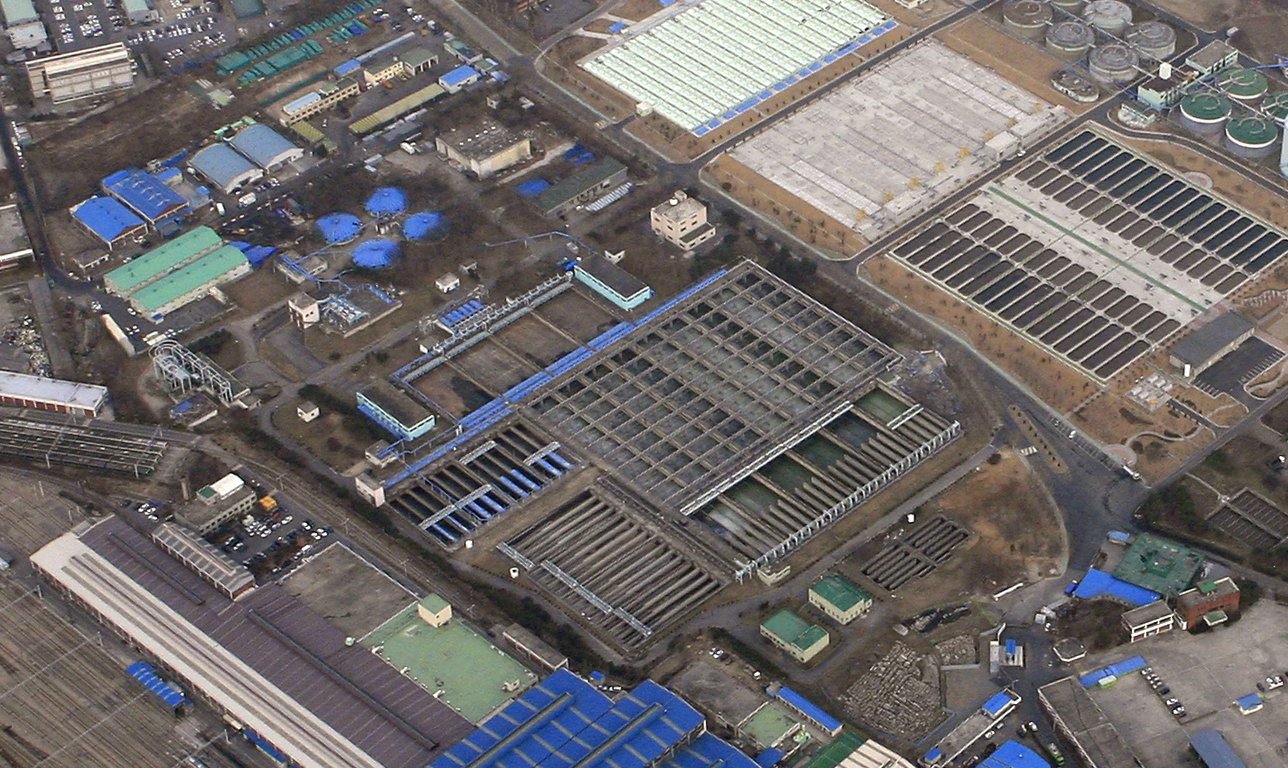

Three sequential upflow biofiltration stages
-
Stage 1
The first biofilter replaces conventional primary clarifiers to optimize suspended solids removal
-
Stage 2
The second biofilter performs biological denitrification using carbon diverted from the first staged, followed by aerobic oxidation of organic compounds.
-
Stage 3
The third biofilter performs aerobic nitrification and recycles nitrates back to the denitrifying second stage.
Exceptional Performance
Over six months, performance of the new Proteus biofiltration system maintained or exceeded treatment targets averaging:
61% Reduction in Suspended Solids
43% Reduction in BOD
24% Reduction in Total Phosphorus
Performance Data
Parameter
BOD5
TSS
TN
TP
Influent
120
102
33
3.1
Permit
10
10
20
0.5
Plant Effluent
1.4
2.5
13
0.23
Shrink footprints while increasing treatment capacity
Hydraulic residence time (from primary through tertiary treatment) averaged 3.5 hours, a 70% reduction from the previous average of 11 hours.
The footprint of the new treatment train was reduced by 64%, while primary treatment alone achieved an 80% footprint reduction.
Reclaim valuable space
Retrofitting even parts of its treatment train in land-limited water recovery facilities can free up significant land resources for additional treatment or property development, without increasing operating costs. This could enable space-constrained plants to achieve goals such as biological nutrient removal or onsite advanced treatment for the first time.